Continuous Filament Mat for PU Foaming
FEATURES & BENEFITS
● Very low binder content
● Low integrity of the layers of the mat
● Low bundle linear density
PRODUCT CHARACTERISTICS
Product Code | Weight(g) | Max Width(cm) | Solubility in styrene | Bundle density(tex) | Solid content | Resin compatibility | Process |
CFM981-450 | 450 | 260 | low | 20 | 1.1±0.5 | PU | PU foaming |
CFM983-450 | 450 | 260 | low | 20 | 2.5±0.5 | PU | PU foaming |
● Other weights available upon request.
● Other widths available upon request.
● CFM981 has very low binder content, which can be evenly dispersed in PU matrix during foam expansion. It’s an ideal reinforcement material for LNG carrier insulation.
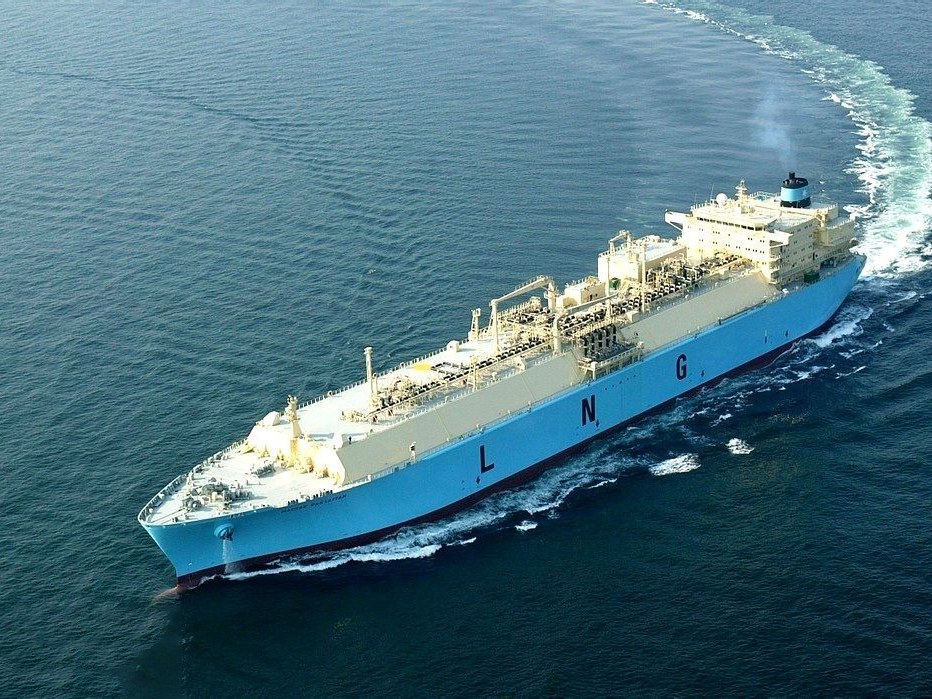
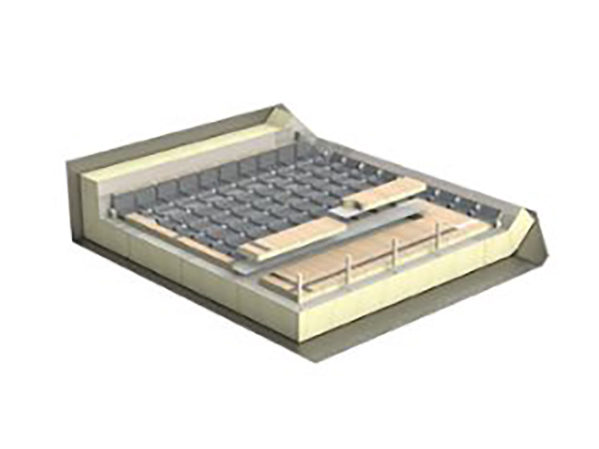
PACKAGING
● Inner core options: Available in 3" (76.2mm) or 4" (102mm) diameters with a minimum wall thickness of 3mm, ensuring adequate strength and stability.
● Protection: Each roll and pallet is individually wrapped with protective film to safeguard against dust, moisture, and external damage during transportation and storage.
● Labeling & Traceability: Each roll and pallet is labeled with a traceable barcode containing key information such as weight, number of rolls, manufacturing date, and other essential production data for efficient tracking and inventory management.
STORAGING
● Recommended storage conditions: CFM should be kept in a cool, dry warehouse to maintain its integrity and performance characteristics.
● Optimal storage temperature range: 15℃ to 35℃ to prevent material degradation.
● Optimal storage humidity range: 35% to 75% to avoid excessive moisture absorption or dryness that may affect handling and application.
● Pallet stacking: It is recommended to stack pallets in a maximum of 2 layers to prevent deformation or compression damage.
● Pre-use conditioning: Before application, the mat should be conditioned in the worksite environment for at least 24 hours to achieve optimal processing performance.
● Partially used packages: If the contents of a packaging unit are partially consumed, the package should be properly resealed to maintain quality and prevent contamination or moisture absorption before the next usage.