Fiberglass Continuous Filament Mat
Jiuding mainly offers four groups of CFM
CFM for Pultrusion
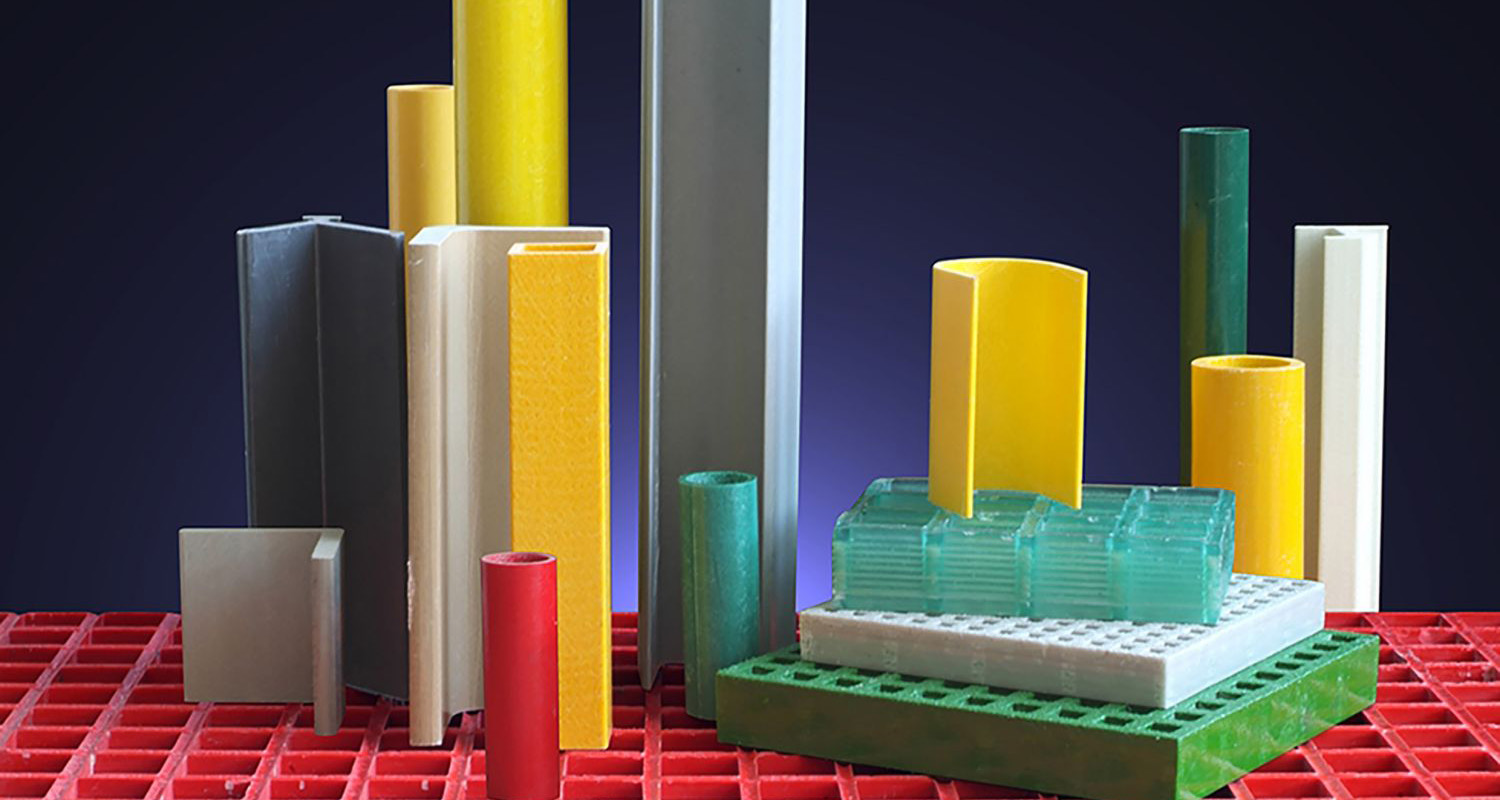
Description
CFM955 is ideally suited for manufacture of profiles by pultrusion processes. This mat is characterized as having fast wet-through, good wet-out, good conformability, good surface smoothness and high tensile strength.
Features & Benefits
● High mat tensile strength, also at elevated temperatures and when wetted with resin, Can meet fast throughput production and high productivity requirement
● Fast wet-through, good wet-out
● Easy processing (easy to split into various width)
● Outstanding transverse and random direction strengths of pultruded shapes
● Good machinability of pultruded shapes
CFM for Closed Molding
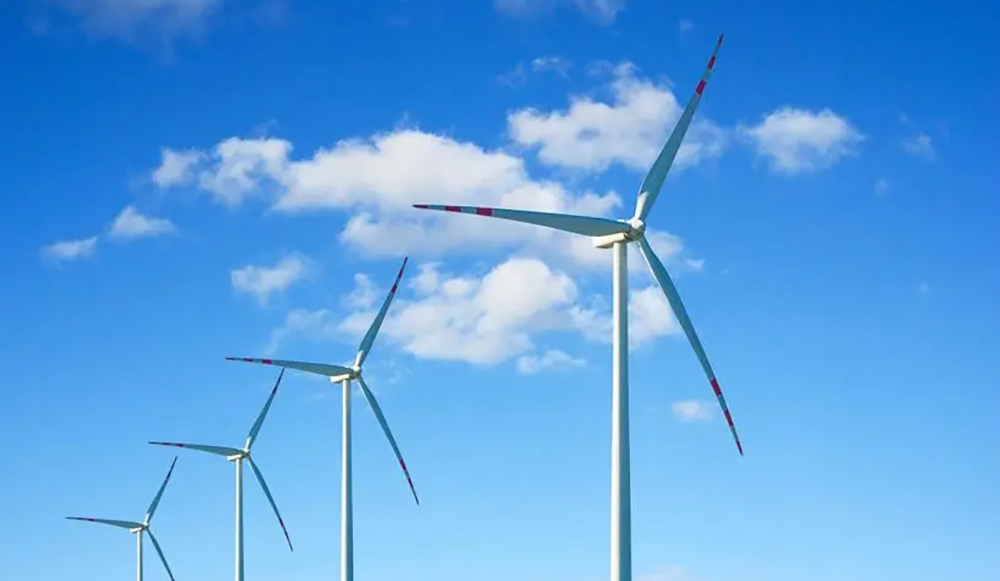
Description
CFM985 is ideally suited for the infusion, RTM, S-RIM and compression processes. The CFM has outstanding flow characteristics and can be used as reinforcement and/or as a resin flow media between layers of fabric reinforcement.
Features & Benefits
● Outstanding resin flow characteristics.
● High wash resistance.
● Good conformability.
● Easy unrolling, cutting and handling.
CFM for Preforming
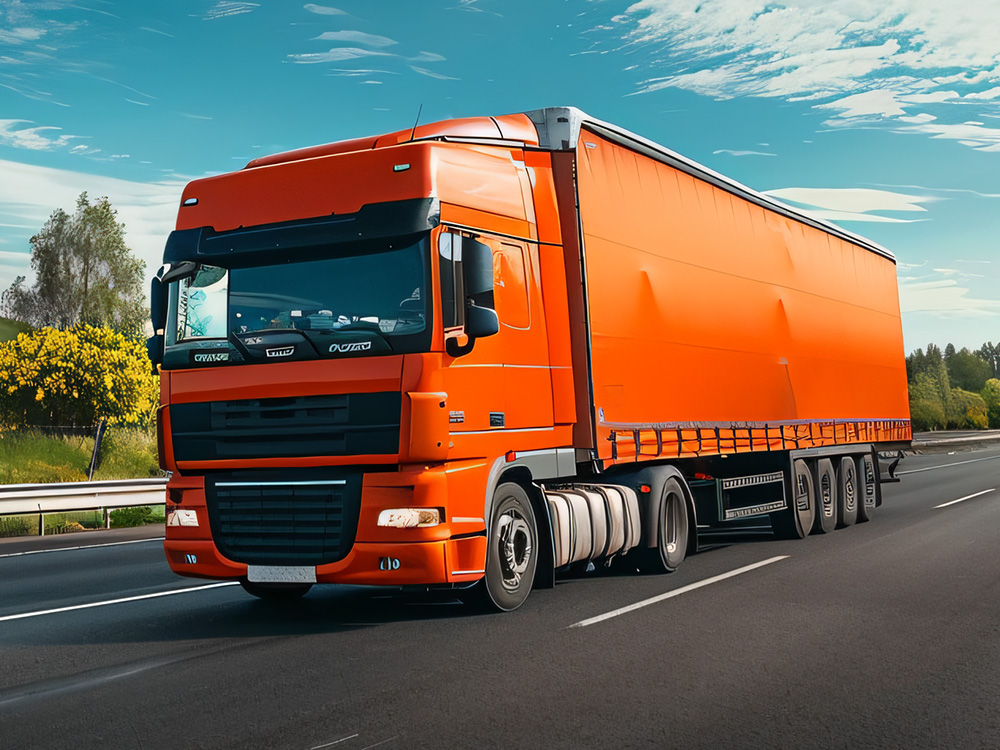
Description
CFM828 is ideally suited for preforming in closed mold process such as RTM (high and low- pressure injection), infusion and compression molding. Its thermoplastic powder can achieve high deformability rate and enhanced stretchability during preforming. Applications include heavy truck, automotive and industrial parts.
CFM828 continuous filament mat represents a large choice of tailored preforming solutions for closed mold process.
Features & Benefits
● Provide an ideal resin surface content
● Outstanding resin flow
● Improved structural performance
● Easy unrolling, cutting and handling
CFM for PU Foaming
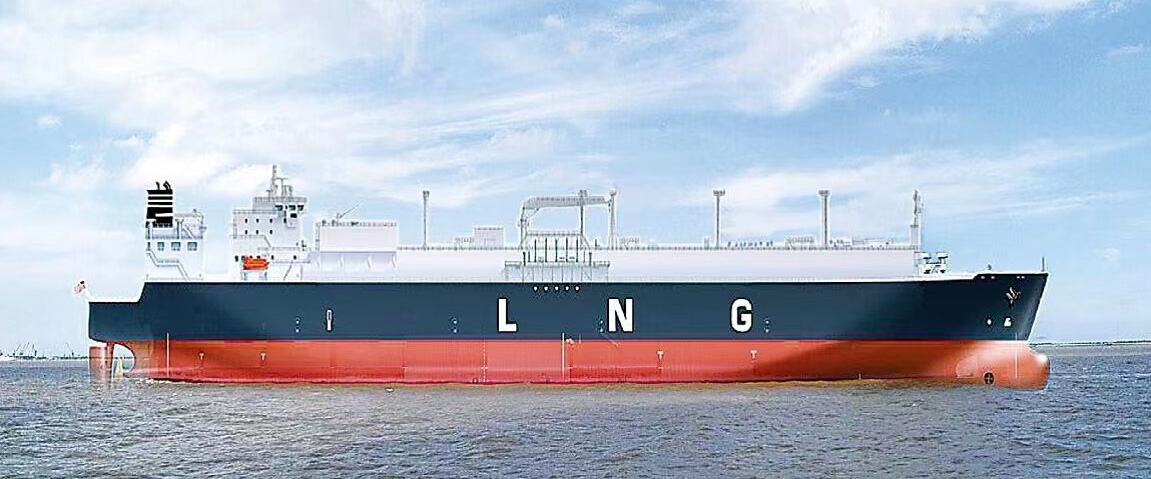
Description
CFM981 is ideally suited for polyurethane foaming process as the reinforcement of foam panels. The low binder content allows it to be dispersed evenly in PU matrix during foam expansion. It’s an ideal reinforcement material for LNG carrier insulation.
Features & Benefits
● Very low binder content
● Low integrity of the layers of the mat
● Low bundle linear density